Ceramic Grade Sodium Carboxymethyl Cellulose (CMC) is a crucial ingredient in modern ceramic production. Its ability to improve the viscosity, stability, and performance of ceramic materials makes it an essential additive for manufacturers.
Q1: What is Ceramic Grade Sodium Carboxymethyl Cellulose (CMC)?
A1: Ceramic Grade Sodium Carboxymethyl Cellulose (CMC) is a specialized type of CMC used primarily in the ceramics industry. It is a cellulose derivative that is used as a binder, thickener, and stabilizer in ceramic formulations. This grade of CMC has been tailored to meet the specific needs of ceramic production, where it helps enhance the quality, consistency, and performance of ceramic products such as tiles, sanitary ware, and porcelain.
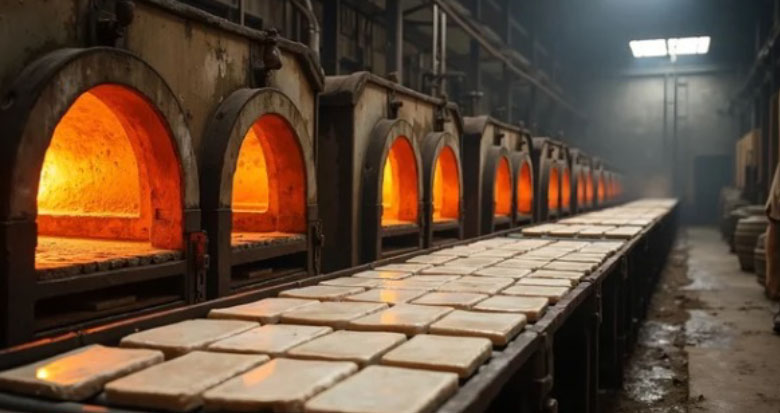
Q2: What are the main applications of Ceramic Grade CMC?
A2: Ceramic Grade CMC plays a critical role in various stages of ceramic production:
- Tile Production: In tile manufacturing, CMC acts as a binder and thickening agent, improving the handling properties of the tile body, ensuring proper shaping, and enhancing the overall strength of the tiles.
- Glazing and Coatings: CMC is often added to ceramic glazes and coatings to enhance their smoothness, viscosity, and stability. It helps to ensure an even distribution of glaze and prevents sedimentation.
- Casting and Molding: Ceramic Grade CMC is used in the preparation of slip (the liquid mixture used for casting) by increasing its viscosity, which improves the flowability and reduces water loss during molding.
- Improving Rheological Properties: CMC helps control the viscosity and rheological behavior of ceramic pastes, ensuring optimal processing properties and consistent quality.
Q3: How does Ceramic Grade CMC improve the production process of ceramics?
A3: Ceramic Grade CMC enhances the ceramics production process in several key ways:
- Improved Workability: CMC helps improve the workability of ceramic bodies by making them more cohesive and easier to shape. It provides the necessary plasticity for molding and forming.
- Increased Strength and Durability: As a binder, CMC improves the strength of the dried ceramic product and reduces the risk of cracking or breakage during firing.
- Reduced Water Loss: During the drying process, CMC reduces water evaporation, which helps control shrinkage and cracking of the ceramic pieces.
- Enhanced Glaze Uniformity: CMC ensures that the glaze adheres uniformly and smoothly to the ceramic surface, improving the final appearance and durability of the product.
Q4: What are the key benefits of using Ceramic Grade CMC?
A4: The key benefits of using Ceramic Grade CMC include:
- Enhanced Viscosity Control: CMC allows for precise control over the viscosity of ceramic slips, pastes, and glazes, which is essential for high-quality production.
- Improved Product Quality: By improving the texture, consistency, and strength of the final product, Ceramic Grade CMC contributes to the production of ceramics with superior performance and durability.
- Cost-Effective: By improving the efficiency of the production process and reducing material wastage, Ceramic Grade CMC helps to reduce overall production costs.
- Environmentally Friendly: As a natural polymer derived from cellulose, CMC is biodegradable and environmentally friendly, making it an attractive choice for manufacturers seeking sustainable solutions.
As demand for high-quality, efficient, and eco-friendly ceramic products grows, the role of Ceramic Grade CMC will continue to be vital in achieving superior results.
SINOCMC Team